In-Context AI-Driven Support for Operators and Technicians
With so many steps and variables on the production floor, it’s easy to miss a detail, causing delays, rework, or safety risks.
AutoAlign Visor delivers real-time, hands-free support by guiding operators with step-by-step instructions, visuals, and checks directly in their line of sight. AI verifies tasks in real time using the built-in camera, helping teams work faster, reduce errors, and stay on track.
AutoAlign Visor delivers real-time, hands-free support by guiding operators with step-by-step instructions, visuals, and checks directly in their line of sight. AI verifies tasks in real time using the built-in camera, helping teams work faster, reduce errors, and stay on track.
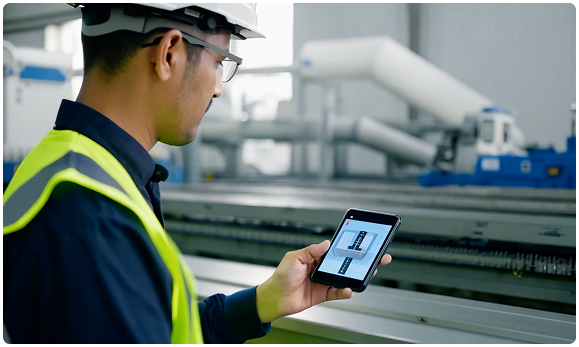
More Effective Quality Assurance and Control
Visor overlays checklists, visual standards, and alerts directly on equipment, helping operators catch defects before products leave the line. Technicians can access AI-powered training, pull up resources instantly, or learn interactively from remote experts.
When training and information access are limited, it drives up costs through rework, downtime, and damaged reputation.
When training and information access are limited, it drives up costs through rework, downtime, and damaged reputation.
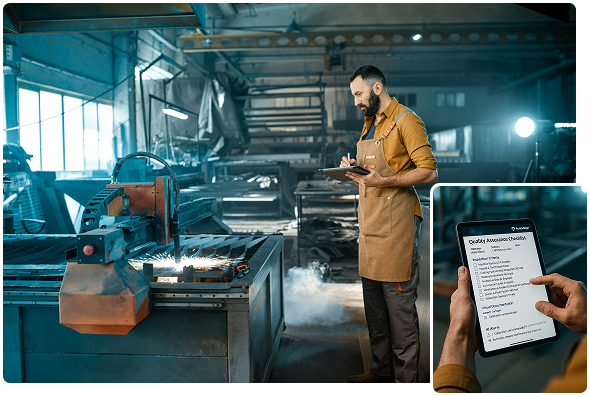
Automated Issue Detection and Root Cause Analysis
Technicians instantly access 3D models, repair guides, and remote support via Visor’s AR, reducing delays and troubleshooting time.
Visor helps engineers resolve issues faster with live machine data, step-by-step tutorials, or remote expert guidance.
Visor helps engineers resolve issues faster with live machine data, step-by-step tutorials, or remote expert guidance.
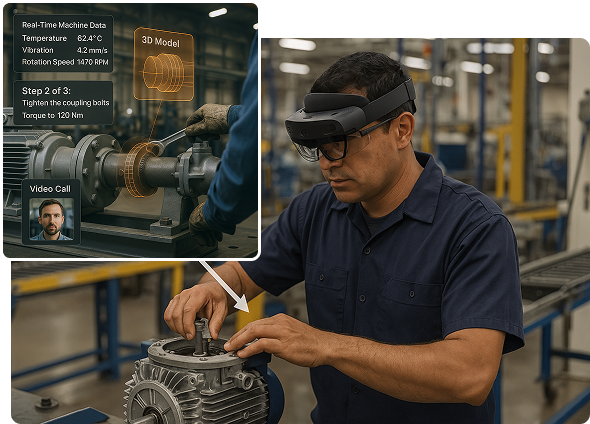
Compliance and SOPs
Provide in-context guidance for complicated SOPs and monitor adherence to procedures, recording compliance
Alert proactively when there are deviations or safety issues detected.
Alert proactively when there are deviations or safety issues detected.
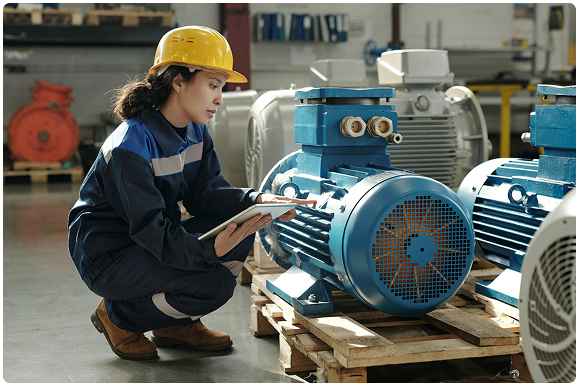
Workplace Safety, Incident Reporting & Prevention
The lack of training, experience, and access to information increases costs whether in the form of ineffective repairs, lost reputation or follow-up visits.
AutoAlign Visor allows effective training on-site. Technicians get interactive, AI-powered feedback, can bring up resources quickly, or learn interactively from remote instructors or senior staff.
AutoAlign Visor allows effective training on-site. Technicians get interactive, AI-powered feedback, can bring up resources quickly, or learn interactively from remote instructors or senior staff.
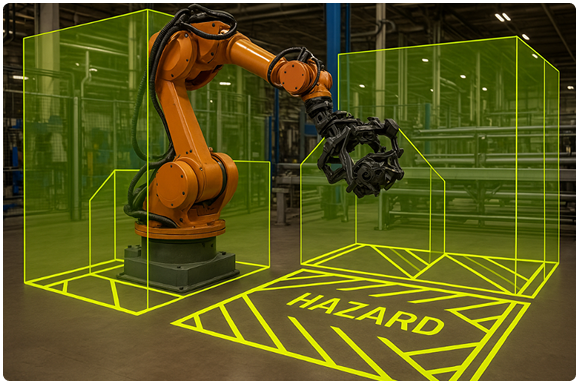
Technical Assistance & Troubleshooting
Visor utilizes visual and sensor data to deliver in-context support and real-time troubleshooting. It can retrieve reference materials, guide technical diagnostics, verify parts, and proactively alert users when something is incorrect, all in the moment, right where work happens.
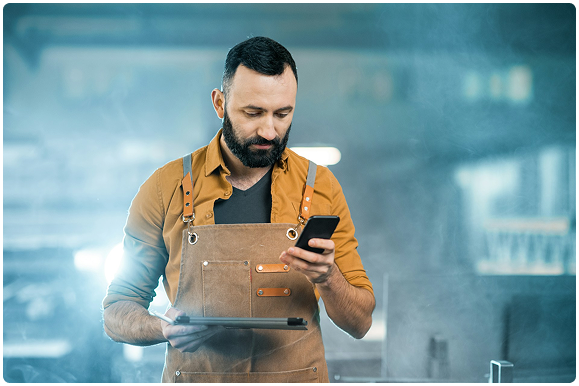
Technical Assistance & Troubleshooting
Traditional onboarding can delay productivity. With AutoAlign Visor, workers see instructions and training overlaid on equipment, access training videos, and call remote mentors as they learn by doing — without stopping the line.
AR-based in-context training with AutoAlign Vizor offers a more efficient approach to instruction. With Visor, new employees can easily bring up and view step-by-step instructions and visual aids overlaid on the equipment they need to assemble and operate.
AR-based in-context training with AutoAlign Vizor offers a more efficient approach to instruction. With Visor, new employees can easily bring up and view step-by-step instructions and visual aids overlaid on the equipment they need to assemble and operate.
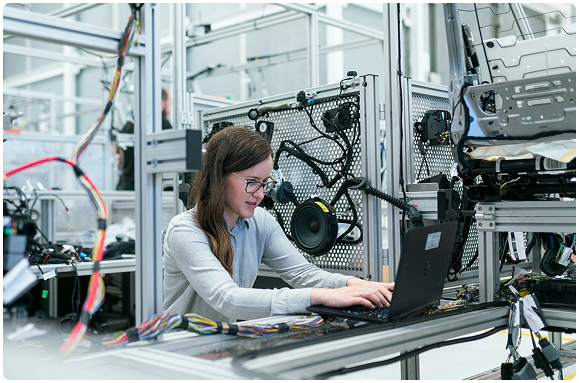